Then and Now: Optimize Your Fault Detection and Diagnostics Results
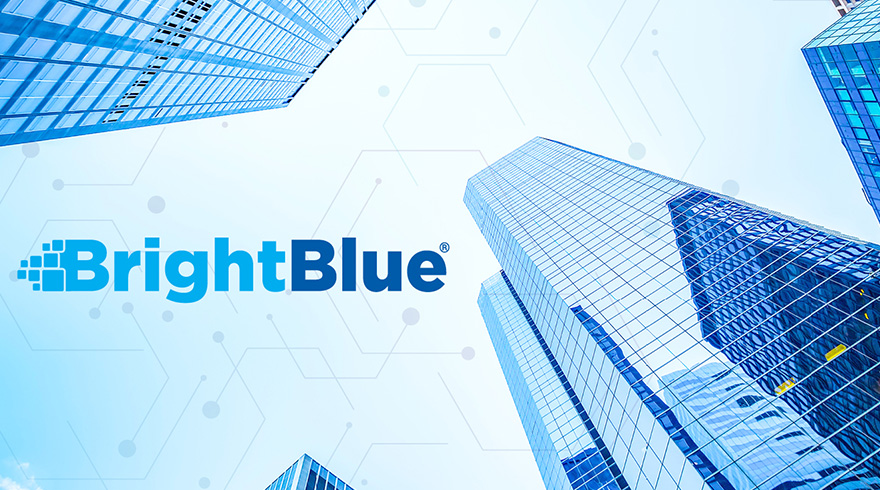
Fault detection is a crucial component to a facility’s building automation system (BAS) or building management system. Fault detection assists building operators in understanding issues that need to be addressed within the core systems for HVAC, electrical, security and fire systems. The role of the BAS is to monitor and control the primary equipment within a large building. Through this control system, a building operator views the facility’s data and makes decisions on how best to address any equipment or performance issues.
Equipment monitoring for those systems results in a LOT of data every day. What happens with all that data? How is it managed and optimized? A smart analytics software solution helps building operations teams better manage their data and achieve increased efficiency and optimal levels of comfort, occupant health and energy savings.
The Way It Was, Then
For years, operators have struggled to chase problems as they occur: an alert sounds, an operator rushes to assess the problem, and when critical, takes action immediately, or otherwise, logs incidents in reports. This results in a continuous reactive cycle of inefficient and ineffective system procedures and outcomes, with teams reacting only to what’s failed and struggling to analyze and prioritize large amounts of data.
From BAS data, building operations teams continually create spreadsheets or system reports for review and planning and then build maintenance calendars based on manufacturer recommendations and warranty schedules. Operators must decide which data to review, and when, and then analyze it for meaning. BAS systems bring controls to one central place for operator management and efficiency. Yet without real-time sensors, monitoring and pinpoint diagnostics, teams still can only react to faults as they occur rather than predicting and preventing problems before they affect performance.
Lessons Learned
The data produced through the BAS or central plant is critical, and the key to what happens after we obtain that data is of utmost importance. Understanding and detecting faults is critical to extending the life span of a building’s core systems. Without it, overwhelming data can delay timely solutions. Through embracing smart analytics technology, operators can now predict where faults are likely to occur and shift to an integrated, real-time building management approach.
Improved Diagnostics Means Big Results, Now
Today, companies are striving to implement proactive and predictive maintenance models into building management procedures. This vision opens the door to innovative opportunities within the BAS by adding a layer of diagnostic capabilities to fault detection.
According to the Clockworks Analytics and Nexus Labs Building Analytics Comparison Guide, the three main steps to reach optimal fault detection and diagnostics (FDD) are:
Analysis Accuracy
Analysis accuracy helps put each fault into context so it is understood in relation to other detected anomalies. Each additional fault should take the first into account before diagnosis.
Automated Root Cause Analysis
This component prioritizes faults to determine the root cause and suggested actions to solve it — a crucial part of maintaining a holistic understanding of FDD.
Automated Prioritization
Through automating the diagnostic process, the building operator is now able to understand the impacts these faults have on energy, comfort and maintenance.
The FDD process is easily implemented into an existing BAS or central plant with help from a trusted Smart Analytics provider working alongside a building operations team.
Beyond Fault Detection: What's Next for Building Automation?
Not only does Fault Detection and Diagnostics increase efficiency of major systems and operational procedures, it increases tenant satisfaction and productivity. Smart Analytics data is continuously gathered and monitored throughout a building or campus, so temperature or humidity variances that could affect comfort are seen and resolved before they can be reported. This allows occupants to work undistracted and keeps technicians or operations staff from chasing reported issues.
Well maintained equipment that works at optimal levels ensures a healthy work environment, producing a more effective business dynamic for your building’s tenants while also ultimately conserving energy, reducing utility costs and helping your organization achieve its sustainability goals.
These pieces all function in tandem to support facility operations to optimize building performance. By uncovering the blind spots within core operational functions, we can now focus attention on what matters most — your core business. Moving beyond the capacity of a standard BAS, powerful data analytics are the future of enhanced building automation.
Go from reactive to proactive with Smart Analytics
More from the Blog
How AI in BrightBlue Works
While AI has been all over the headlines recently, the history of artificial intelligence goes back...
Benefit the Planet and Save Money with AI-Enabled HVAC Analytics
As businesses and buildings move toward sustainability, the intersection of technology and environmental...
Five Reasons 2025 Is the Year of Planned Building Maintenance
If you’ve spent much of this week staring at your 2025 building operations budget looking for...
Subscribe to our blog
Please provide your email address to subscribe!